Discover new things – your knowledge advantage with us.
Welcome to our blog! Here we share exciting news, inspiring case studies, and practical knowledge on topics that move your industry. With our posts, we aim not only to inform but also to provide food for thought and support you in making informed decisions. Dive into a world full of expertise, innovation, and insights that truly matter.
Quickly find what interests you.
Discover interesting downloads now.
In this white paper, we explain the developments in the field of artificial intelligence for sorting and show how you can benefit from it to make your processes more precise, sustainable, and profitable.
In this white paper, we explain the various maintenance strategies with a focus on predictive maintenance and provide an outlook on how AI-driven predictive maintenance can make your production more efficient and thereby improve food safety.
This White Paper explains what is important for recyclates and what measures are necessary to establish a future-proof process landscape for the use of recyclates.
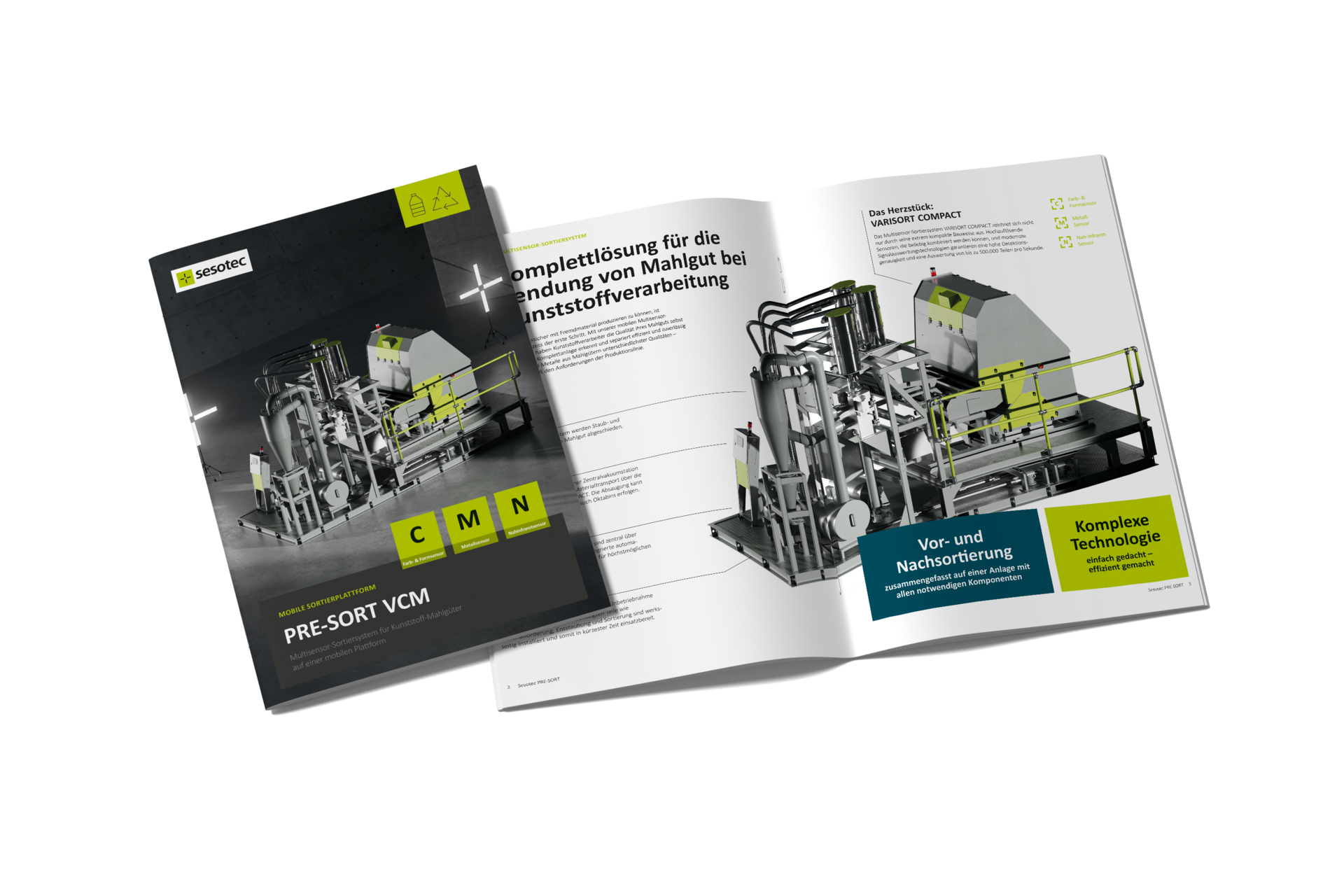