Compliant Production in the Food Industry
The innovative software for seamless and efficient documentation
Food safety demands perfection. Our software ensures seamless and efficient documentation in food production, featuring Audit Check, Sensitivity Prediction, Compliance Mode, Integrated Compliance Monitoring, and Integrated Validation Process.
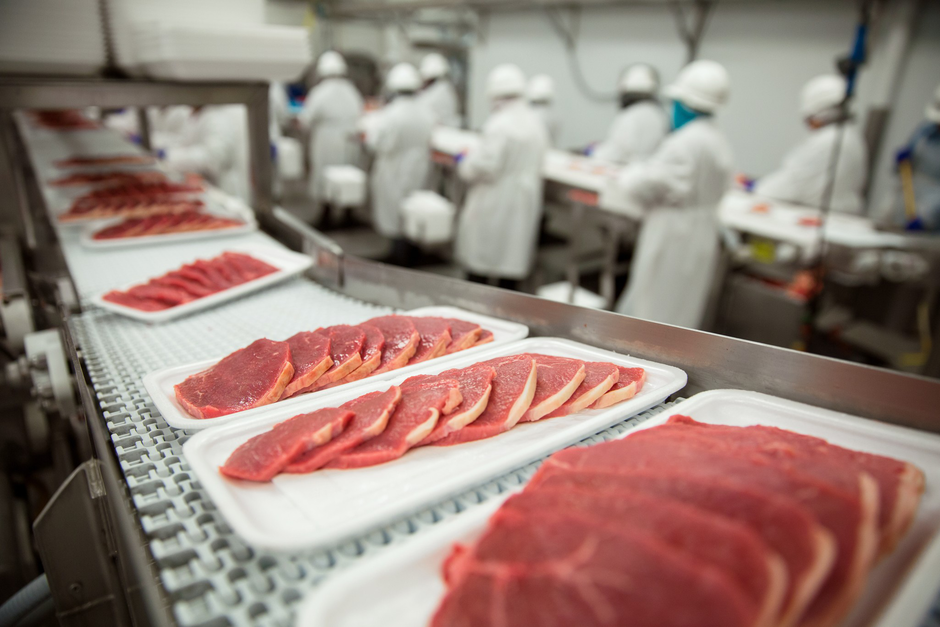
Your Challenges...
As a food manufacturer, product quality is your top priority. You're also legally required to meet a wide range of food standards. This immense responsibility means that even the smallest mistake can be costly and significantly damage your reputation. Product recalls, liability claims, and consumer harm are just a few potential consequences of faulty products.
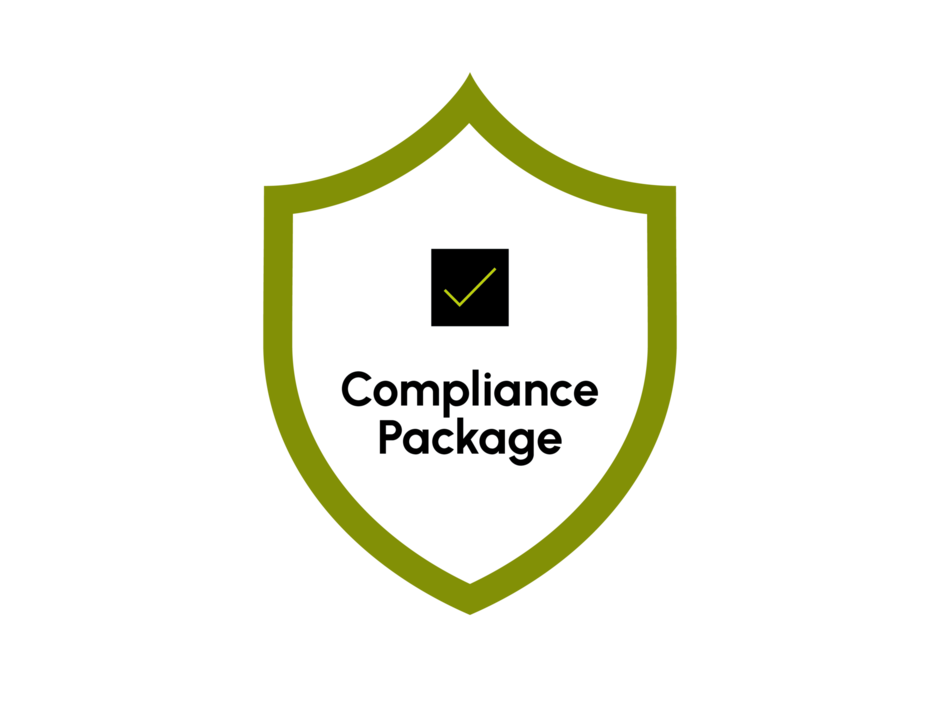
...our solutions
We want to ensure you sleep soundly at night—that's why we've developed the Sesotec Compliance Package, a comprehensive solution for food safety. This package not only guarantees regulatory-compliant food production, but also offers process security when launching new products, ensures your machines operate flawlessly, reduces product waste, and protects you from tampering with paperless in-machine documentation.
Mobile. Precise. Efficient.
Compliance Package Features
Quality Assurance 4.0: The Audit Check guides you through the audit routine with a step-by-step assistant, logging every action. This continuous quality monitoring is crucial for food producers and processors to ensure consistently high product quality.
The 3 Steps of the Audit Check
1. RequestThe prompt to perform the Audit Check appears on the Control Unit display. You can manually set the frequency of this prompt.
- Hourly
- Daily
- Interval
- Product Counter
- Product Change
2. Audit Check
Test bodies must be conveyed as shown in the dialog window. You can manually select and set the material type, diameter, and maximum allowable signal strength.
3. Result
The results of each test body and the overall inspection are transferred to the logbook and saved.
The Sensitivity Prediction is automatically calculated after each learning process and after changes to sensitivity-dependent parameters, enabling an automatic determination of the detection sensitivity for various foreign bodies.
Sensitivity Prediction in X-ray Inspection
The "Sensitivity Prediction" allows for the automatic determination of detection sensitivity for stainless steel and glass during X-ray inspection. The 100 test cards made of glass and stainless steel are stored in all sizes within the software. They are processed with the grayscale image of the product as if a product with a test card were actually being conveyed. All information on detection sensitivity is calculated from these generated images and displayed in a graph.
Sensitivity Prediction in Metal Detection
After the learning process, the software automatically indicates the most suitable Inspection Level (IL) with corresponding sensitivities for iron, stainless steel, and non-ferrous metals. The IL with the predicted sensitivities that best meet customer requirements can then be selected.
Benefits for the Customer
- Immediate overview of sensitivity levels
- Easy comparison with required detection sensitivity
- Significant time savings during the learning process
- Simple determination of the best Inspection Level for the product under examination
In Compliance Mode, sensitivity can be adjusted at the touch of a button to meet factory or audit standards, ensuring compliant production while reducing the false reject rate. This maintains consistent process stability.
Reduction of False Reject Rate (F.R.R.) & Minimization of Good Product Loss:
The X-ray device adjusts the software filters during the learning process in Compliance Mode to reliably detect the specified test objects.
The metal detector adjusts the trigger threshold of the set product to reliably detect the specified test objects.
Benefits for the Customer
- Compliance with food safety standards
- Savings on labor, packaging, and product waste
- Increased production efficiency
- Display of predicted performance and compliance values for easy verification
- For X-ray inspection systems: less retraining with challenging products
Integrated Compliance Monitoring ensures your inspection system's detection capabilities are always on point. This continuous internal oversight of detection requirements allows for immediate identification of discrepancies, enhancing the stability of your production process.
Customer Benefits
- Compliance with food safety standards
- Save time, packaging, and reduce product waste
- Boost production efficiency
- Enhance product quality
- Minimize the risk of poor quality control and record-keeping
How It Works for Metal Detection
- The detector is monitored by an internal test signal, tailored to the product during the learning process.
- Performance forecasts and compliance values are displayed for quick and easy verification.
- If received information doesn't meet specific requirements, the system triggers an error or warning message based on configuration.
How It Works for X-ray Inspection
- Initial sensitivities are calculated and stored immediately after the autotrain process.
- The current sensitivity for stainless steel and glass is continuously and automatically checked at set intervals.
- Sensitivity limits can be manually adjusted.
- If limits are exceeded, an error or warning message is triggered.
The Integrated Validation Process (IVP) is a documentation tool that proves your product meets the desired quality standards. The ultimate goal of the Integrated Validation Process is a certificate from Sesotec detailing the validation results.
Customer Benefits
- Consistent validation
- Automatic backup of all settings to restore the device to its validated state
- Recordings in the metal detector
- Establish realistic testing standards and ensure compliance
- Reliable report data
- Automatic notifications for the next validation, eliminating the need for washable stickers
- Certificate can be saved as a PDF on a USB stick
*Customers can independently validate new products through guided menus and receive a "Report of Validation," which does not replace the validation certificate required for the annual audit by an external service provider (manufacturer).
Service Offering
For all existing systems (types G+, Primus+, GO, Intuity), our service offers manufacturer validation as a service. This includes the creation of the annual validation certificate and a maintenance report. It involves a repeat test of the Probability of Detection (P.O.D.) at the most challenging point of the metal detector using specified test bodies.
Customer Advantages
- Execution of repeat tests including evaluation and documentation
- Determination of threshold values to provide additional security during daily routine checks.
Interested?
Get all the details on our Compliance Package in our concise brochure!