Experience Sesotec Live
Our trade fair appearances offer you more than just a presentation – they are a platform for dialogue, innovation, and inspiration. Visit Sesotec at the world's leading trade fairs and experience our solutions for the industry up close. Whether sorting, inspection, or metal detection: Our technologies ensure the highest efficiency and precision in your processes. Be inspired and find out how we can shape the future together!
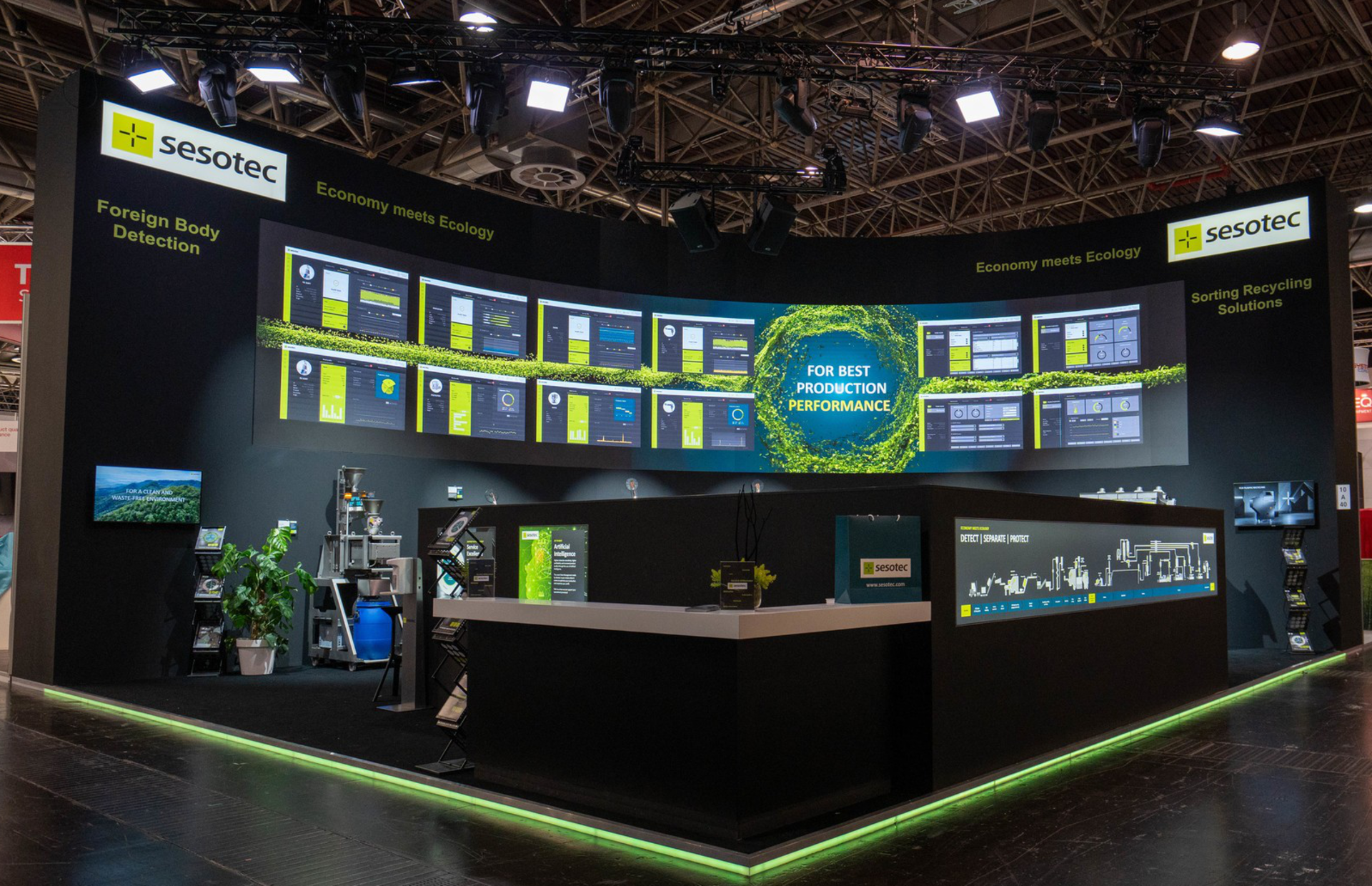
VISIT US
Our next exhibitions
Plastics
PRS Middle East & Asia
9/15/25
-
9/17/25
9/17/25
Dubai, United Arab Emirates
Recycling
Recycling Expo
9/16/25
-
9/18/25
9/18/25
Warsaw, Poland
Plastics
RUBBERTECH CHINA
9/17/25
-
9/19/25
9/19/25
Shanghai, China
Can't make it to the fair?
No problem – there are many more ways to experience Sesotec live! Visit us in one of our showrooms worldwide or see our solutions in action in our in-house test center. Our experts look forward to showing you customized solutions for your requirements.